
High-precision in-line viscosity meter for the cosmetic and chemical industry Our product managers can help you determine the most reliable and best-performing choice. The vibration technique is very accurate, can be easily integrated into the process (small, pin-shaped) and does not suffer from process vibrations or flow changes. Often the entire process needs to be adjusted to make an in-line measurement possible. In addition, the technology is less easy to integrate into the process. Rotational techniques are more bothered by process fluctuations or vibrations and flow changes. The viscosity meter then determines the viscosity of the measuring liquid. Rotation: A spindle (cylinder or disk) is immersed in the fluid to be examined and then the force that the spindle needs to overcome the inertia of the fluid is measured. The liquid to be measured is located in the annular (annular) space between the two cylinders Torsion: in a torsional balance, the deflection is measured between two cylinders, the interior of which rotates at a fixed speed. Vibration: A resonator is immersed in a liquid and the degree of damping from the liquid is measured to determine the viscosity.
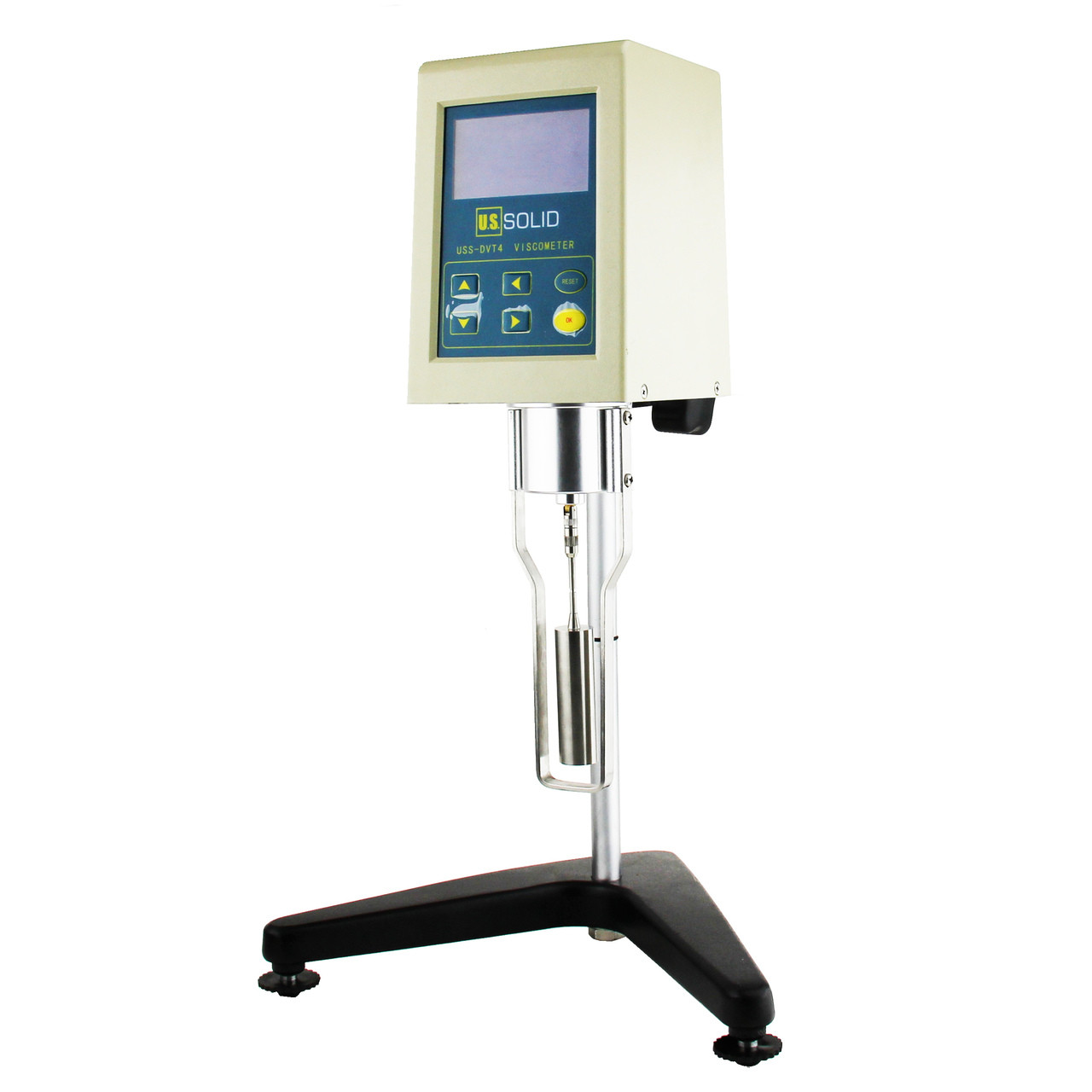
These methods are used for all types of liquids, pastes and slurries. There are various methods for an in-line viscosity measurement suitable for chemical and cosmetic processes, such as rotation, vibration and torsion. What are the methods for measuring in-line viscosity for the cosmetic and chemical industry? And how do I choose the right one?īut how do you know what the right in-line viscosity analyzer is for your process? After all, there are different analyzers on the market that use different measuring methods that can be used in-line in chemical and cosmetic processes. Thanks to the Sofraser sensor, unexpected pavements that stop production no longer disrupt the process and production and sales losses are minimized. Production efficiency has also increased. Employee stress caused by too rapid hardening is now avoided, in addition to the fact that the MIVI sensor offers stability and ensures a consistently high quality of our products. NL Rolpin: “Every operator feels more comfortable now that the MIVI viscometer has been installed. Especially in this time of rising material costs, the increasing number of competitors, the higher expectations of the customer and the desire to produce in a more environmentally conscious way, chemical and cosmetic companies can make a lot of profit with an (in-line) viscometer. Also in the production of complex liquids such as coatings, paints and inks, an in-line viscosity meter is desirable to achieve the desired fluidity, thickness and image characteristics within strict parameters. In a number of production processes it is precisely for each product that a different viscosity is required to give it the correct stability, for example architectural glass and wall elements made of acrylic and/or polymer. For example, a better flow through tubes can take place and dispensers can be adjusted to the right force to induce flow without the package becoming overfilled. But in addition to quality control, knowing the viscosity of a (semi) finished product helps to organize the production process efficiently and to reduce costs. By measuring the viscosity of products such as toothpaste, cough syrup or ointment, ink, paint and coatings, manufacturers can predict how products will behave once they are in the hands of the consumer. In the chemical and cosmetic industry, viscosity testing is a very important parameter for quality control.


What are viscosity meters used for in the chemical and cosmetic industry?
